Regenerative Thermal Oxidizers – RTOs are used to capture and eliminate VOCs from an air stream.
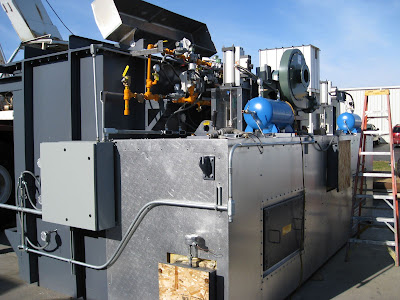
Thermal treatment of VOC's and other air pollutants works by a simple reaction of the harmful air pollutants with oxygen and heat. In this environment the VOC's are converted to CO2, water vapor (H2O), and usable heat. These harmless by-products are released to atmosphere or use an energy recovery technique to further lower the operational costs.
UTI and its personnel have years of VOC's experience and have developed, through years of experience, process strategies and system configurations:
- Solvent Handling, including VOCs Emission Reductions and Recovery
- Odor Control through various technologies: Scrubbers, Carbon Adsorption, Bio Technology and Thermal Oxidation
- Thermal Oxidation Systems ranging in size from 2,000 cfm to 250,000 cfm
- Solvent Recovery Systems ranging in size from 5,000 cfm to 25,000 cfm
- Bio Technologies up to 30,000 cfm
- Incident Investigation of Failed Systems
- Improved VOC Capture Efficiency for Process Systems
- Provided the Design and Specification for VOC's Emission Reduction Equipment and Systems
- Developed Standard CAD Details for VOC's Emission Reduction Systems
- Redesigned Stack and Source Dampers in Conjunction with VOC's Emissions Reduction Equipment to Improve Process Optimization, Comply with MACT Standards and Reduce Energy Costs
- Optimized Thermal Oxidation Systems
- Specified Solvent Recovery Coil Replacements
- Provided Financial Analysis for VOC's Emission Reduction Systems to Provide the Most Cost Effective System for given Applications
- Provided Incident Investigation for Misapplied VOC's Emission Reduction Systems and Equipment Failures
- Provided Expert Witness for Failed VOC's Emission Reduction Systems
- Provided Solvent Extraction Systems Engineering Design
- Designed Solvent Handling, Storage and Unloading Facilities
- Designed Inline Moisture Process Control Systems
- Developed Pulp & Paper Plant P&ID Drawings for Hazardous Systems
- Created Process Flow Drawings & Mass Balance Tables
- Designed Tether (Life Line) Certification
- Provided Calendaring Roll Design and Consultation
- Design Overhead Material Handling Systems and Hoist Certification
- Engineered Polyester Fiber Handling System
- Created Trim/Weed Conveying System
- Provided Ammonia Engine Room Redesign and Certification
- Designed Sewer System Design
- Construction Management for Chemical Plants, Food Plants and Greenfield Facilities
- Designed Furnace Gas Train Evaluation and Design
- Provided Gas Train Design and Specifications
- Designed and Developed Laminator and Sputter Platform Equipment
- Provided Engineering for an Automotive Plant Expansion